Managing Misperceptions from a Pre-Buy Inspection
To a first time airplane buyer, a picky shop can make your beautifully maintained airplane look undesirable by noting minor issues that can be fixed in less time than it takes to note the discrepancy on the inspection report.
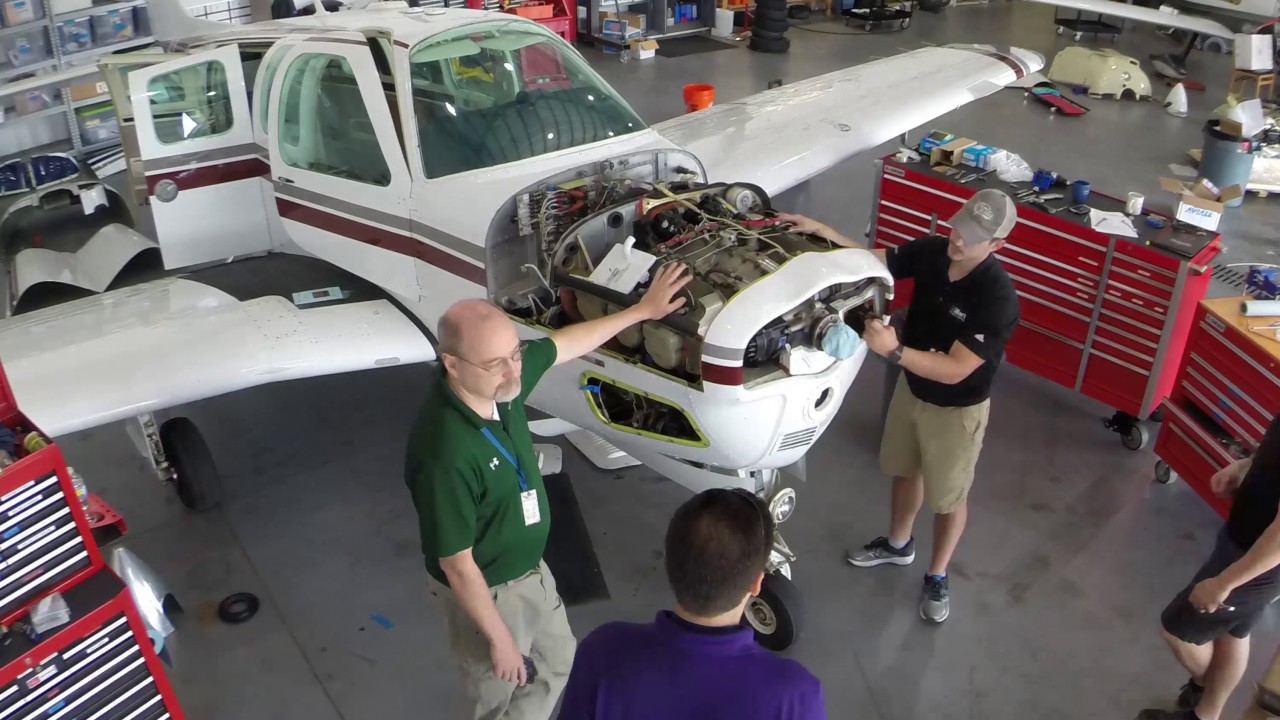
I take a lot of pride in the airplanes I sell to my clients. I want the airplanes squawk free for my buyers, not just for their peace of mind but mine as well. So when it comes to aircraft pre-buy inspections, in my area of the country, there are three Bonanza shops I routinely recommend because I believe they are the very best. And when the aircraft comes out of pre-buy, it has been my policy to rectify any squawks I may have missed.
Having said that, I recently sent a first time aircraft buyer to one of these shops for a pre-buy inspection on an aircraft I owned and was selling. It was a shop I have used many times in the past but not for the past couple of years strictly for logistical reasons. Much to my disappointment, I received an email from the buyer with a PDF attachment of the shop's aircraft inspection report detailing not one or two issues but 67 discrepancies!
My first reaction was obviously embarrassment, however, when I began looking at the actual squawks, my embarrassment turned to anger because only 2 of the 67 involved anything more than minor issues, most of which could have been resolved in the time it took to write up the discrepancy itself. Things like:
1. The tach drive gland nut is loose.
2. No date or tach time is written on the oil filter.
3. One of the right exhaust ball joint springs is broken.
4. The fuel pressure line from the flow divider has a displaced grommet.
5. The exhaust heat muffler shroud is missing one screw.
6. The oil filter adapter is not torqued to spec.
7. The cabin dome light switch is hard to operate.
The next time you have an aircraft for sale and it goes into pre-buy, you may want to consider seeking the buyer's permission to fix the minor discrepancies noted during the inspection process. By pre-authorizing the inspection facility to do this work on your behalf and under a separate invoice, you not only show good faith and reduce the buyer's "to do" list, you eliminate the potential misperception, especially for first time aircraft buyers unfamiliar with the process, that the aircraft may have been neglected when, in fact, it was not.